Digital Twin Technology
Real-time Drilling Engineering
Operation monitoring
Drilling Automation
Operation monitoring
DrillScene® reveals and analyses wellbore conditions, improving performance and preventing unwanted events

Key wellbore/drill string characteristics are configured and used as parameters in the physical models, building a true digital well twin
Configured/modelled trends include hook load, pit volume, SPP, surface torque, cutting transport and more, spanning the key drilling parameters
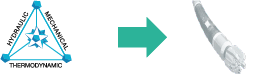
Discrepancies between these parameters allow early discovery of downhole issues and deviations from optimal process parameters

By doing this, DrillScene® is essential to safeguarding and optimization of the drilling operation
DrillScene® analyses well conditions and provides real-time trend analysis, optimizing drilling performance and avoiding unwanted well events
Real-time decision support that is easy to interpret and act on to ensure safe and optimal operations
Proactively avoidance of sidetracks by detection of potential hazards hours before they occur
Real-time simulation of ECD that enables drilling of complex wells with narrow pressure windows
Powered by the underlying Sekal core model
24/7 Remote Monitoring
Sekal provides real-time operation monitoring for its products through the Sekal operation centers.
Digital Twin Technology
A digital twin is developed using Sekal’s sophisticated physical models and utilized to generate trend analysis
REAL-Time Drilling Engineering
Well data is captured and subsequently used to continuously update the digital twin, and thus the trend analysis used by the driller
Operation monitoring
The model is compared against realtime data, to reveal unusual patterns of behavior impacting the drilling operations
Drilling Automation
Insight from the simulation is translated into action; the driller receives decision support and is able to perform efficient and safe drilling